Four proven ways to run a tighter ship at your shop.
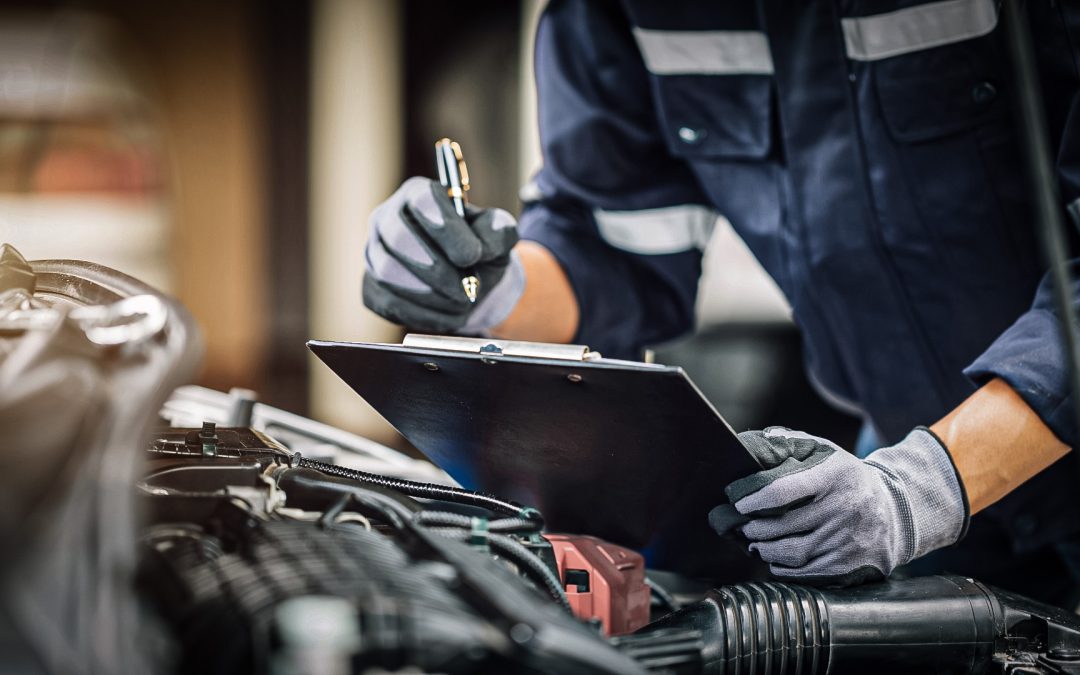
Pete Meier, one of our Dorman Training Center instructors, is a pretty smart cat. Since the day I’ve met him, he’s made it clear that the lab scope is one of his favorite tools and that not using one is a mistake. Now I’ve put a lot of miles on my DVOM over the years, but I am well aware that it’s not always the best tool for the job. In that respect, it’s like a test light—helpful for some stuff, but it doesn’t do as much as a more powerful tool. One test I have avoided over the years is the relative compression test mostly because I didn’t need it—but that is changing.
The relative compression test is a quick-and-dirty way to check compression in an engine. Unlike a traditional compression test, this test doesn’t actually measure the pressure within each cylinder. Instead, one uses the o-scope to monitor the change in starter current draw. A healthy cylinder will make the starter work hard for a bit and draw current as compression rises. A cylinder with a problem, though, will have a different current draw. If compression is low, it will allow the starter to “take a break” and draw less current. If a valve isn’t opening, though, the starter will fight the compression for longer, drawing more current and will appear regularly as an aberration on the scope’s output graph. Seeing the current drawn by each cylinder allows a comparison of the cylinders to one another—hence the test name.
Here’s what a healthy engine looks like when a relative compression test is performed. Photo: Dorman Training Center.
At this stage of the game, I work primarily on antique vehicles. Many are motorcycles. With few cylinders and generally excellent access, the real-deal gold standard of a dry compression test (and a wet one to follow if warranted) is my go-to move on the occasional tractor, Panhead, or 350 that makes its way into my life. This is especially true considering that with decades of service, many of these motors are sacked by the time I see them.
But those are all relics of a bygone era, the compression test included.
We’ve all contorted ourselves and our tools to replace spark plugs in impossible areas—and most compression testers aren’t exactly an easy installation. And while the days of tossing rings in a worn-out engine are past us, carbon buildup hampering proper engine operation is not. In fact, it’s getting worse. Being able to quickly pinpoint a valve that’s not sealing with an amp clamp and taking a few minutes analyzing the scope is obviously more intelligent than trying to remove an intake to access a spark plug hole.
See that low draw every sixth time around? Photo: Dorman Training Center.
Alright, I’m not walking you through a how-to, because there’s a sales pitch at work—I want you to go take Pete’s class. I asked to take this class, and feel super-comfortable suggesting you take it, too. In the interest of full disclosure, I did not pay for it (job perk)—but I would happily.
There were plenty of other suggestions in the “Everyday Scope Testing Techniques” class I thought were great, but to me, learning how to perform this one test alone was worth the price of admission. The o-scope is the same old tool, but learning how to use it in new ways is only one of the topics available on the Dorman Training Center. I’ll get off my sales-guy soapbox, but don’t forget—the cars are changing and it’s up to us to keep up.
The articles and other content contained on this site may contain links to third party websites. By clicking them, you consent to Dorman’s Website Use Agreement.
Participation in this forum is subject to Dorman’s Website Terms & Conditions. Please read our Comment Policy before commenting.