Four proven ways to run a tighter ship at your shop.
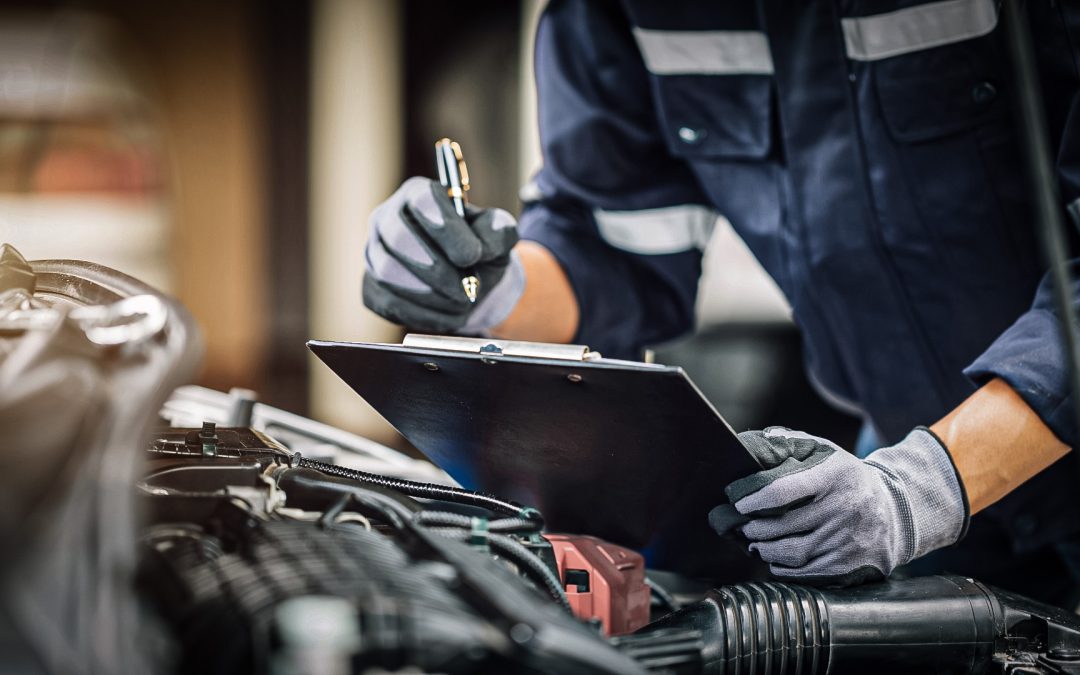
I don’t own a bearing race driver kit, and I haven’t in 20 years of fixing stuff. I also refuse to use sockets to drive a race. I learned a method a long time ago I’ll pass along to you newer techs: I use the race I’m replacing. I primarily have used this trick when servicing trailers, but there are plenty of late model Ford E-series vans and old 2WD trucks still prowling around that need the odd wheel bearing here and there.
It takes longer to write down the steps than it does to just do the job. Use your punch and drive the old race out; this is going to become your tool. Get the new one started somewhat evenly; a scrap of lumber is perfect for this. Sink it flush with the bearing pocket. Grab your old race and some PPE and cut a slice through it with your whizzy wheel. Drive your new race with that. Here’s a good demonstration:
I’d suggest doing just one thing differently. Stack your old race opposite to the way you see here, so the thick side of the old race is butted up against the thin side of the new race. Use that to tap the new race all the way home. If you do it in this manner, you can just grab the punch that’s still laying there from removing the old race and on this go ‘round, due to the slice, one tap sends it back out the way it came in.
Save some money, save your poor sockets, and save some space in your toolbox.
The articles and other content contained on this site may contain links to third party websites. By clicking them, you consent to Dorman’s Website Use Agreement.
Participation in this forum is subject to Dorman’s Website Terms & Conditions. Please read our Comment Policy before commenting.