If you’re still using torque sticks and impact power to install lug nuts and lug bolts, it’s time to reconsider.
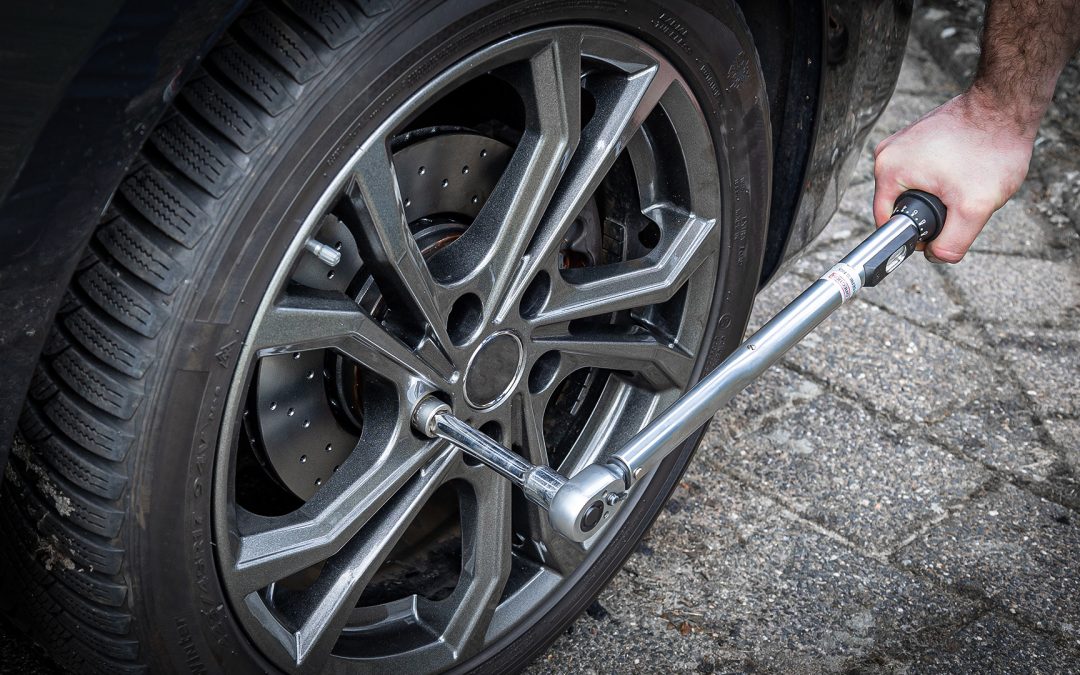
Someone once told me that successful auto repair is a game of inches. But in our fast-paced, ever-evolving industry, inches are no longer accurate—we need to hit the bullseye every time.
Margins are tighter, technology is advancing rapidly, and customer expectations are higher. To stay competitive, we must refine our measurements, fine-tune our processes, and embrace smarter ways of working.
Winning in this challenging and constantly shifting business environment requires more than just skill—it demands adaptability, innovation, and an unwavering commitment to efficiency.
Full transparency: we are a three-bay repair shop that includes me, another full-time tech, and a part-time office manager/secretary. So, we really need to be efficient—there’s no room for wasted time or mistakes. Every second counts, every resource matters, and the difference between success and falling behind lies in how well we optimize our operations. As the old saying goes, it’s not just about working harder; it’s about working smarter.
Here are four tried and true ways that can help make your repair shop more efficient:
It all starts here. When customers walk in, the initial contact is made.
As I built my efficiency arsenal, I began looking at everything. One morning, I sat in one of the office chairs before work, sipping a cup of tea. Did I enjoy the view? I literally framed it with both hands, like a picture frame, and took a look around. What did I see? And what about the view beyond? What did customers notice when sitting in those seats?
Instead of staring at a blank white wall, I put up bookshelves and neatly arranged all the shop’s reference materials. To me, it just looked right. There are over 60 books on that shelf, and even though we rarely use them, customers are often impressed by our “library.” They’ll see books with end flaps dated 1979 and comment on how long we’ve been in business. It’s a small touch that communicates history and expertise.
Then there’s the counter itself. The last thing you want is for a customer to be turned off by having to move a pile of parts just to find the counter. Is it clean and organized for an efficient check-in? Make sure it’s stocked with pens (perhaps ones with your company name and info) and anything else you might need to make the process smooth.
Small touches like these go a long way in creating a positive first impression.
Do you have a “show and tell” section? I’m talking about small parts that demonstrate defects and failures—simple, common stuff. I’ve even labeled a few pieces with the simple question: “What am I?”
Customers, being naturally curious, will spend time handling each one, trying to guess its purpose. Most are wrong, but that’s the fun part! It gives you a chance to interact with them, offering the opportunity to explain what the part is and why it’s important. That’s the “tell.”
The “show” is how it demonstrates the shop’s technical knowledge and understanding of modern vehicles. Customers get to know us through our responses and explanations.
Some of the labeled parts are common failures today: a TPMS sensor with corrosion, a broken rear-view camera, and one of my personal favorites—a brake light switch from a 2009 Cadillac. It’s an unusual part, very high-tech and non-traditional. Customers are often very impressed when we explain it to them.
How many file holding racks does your shop have? Mine has three. One of them is right behind the counter, nestled snugly in the center of the book “library.”
Numbered one through twenty, this rack holds what we call “Hats.” Don’t ask me why we call them that—I think I picked it up from my dentist, and that’s where I got the idea.
The Hat is where everything related to a customer and their vehicle is placed, including signed repair orders, diagnostic reports, safety checklists and parts bills. Anything and everything for that customer, that vehicle, on that day, goes into their Hat.
When it’s time for the final check of the vehicle before release, someone will grab the Hat and go through the close-out process.
One of the best parts of this method? If you’re behind in the shop and need to work from home, you can just grab the Hat on your way out the door. It’s all there.
To be honest, as much as we all try not to work from home, it happens. This system just makes it more efficient and easier. Isn’t that why you’re here?
Remember, I mentioned there are three racks in total? They guide us through the day. Here’s how:
This system matters because it allows me to gauge the shop’s progress at a glance without constantly checking the shop management software reports.
If Rack #2 is full after lunch, I know I’m behind and need to process those parts receipts before afternoon vehicle pickups.
If it’s 2:30 p.m. and Rack #3 still has multiple pending worksheets, we pause and adjust to stay on track.
A repair shop primarily sells two things: parts and labor. That’s it.
Parts are parts—you can’t control their demand, as repairs dictate what’s needed. But labor and time management? That’s a different story.
We’re a three-bay repair shop with enough parking to comfortably fit twenty vehicles. Like any business, we have limits. That’s why I aim to maximize what’s available as efficiently as possible. One way I do this? Clocks. There are nine of them throughout the shop—two in the front office, five in the shop itself, and the rest in key areas like the bathrooms and back room.
Why?
Because I’ve found that a constant, subtle awareness of time affects everyone. When time is always visible, we naturally stay mindful of how long we’ve been working on something—or how long we’ve been on break, on the phone, or distracted by the person who “just stops by.”
You don’t have to be big to make a living—just efficient. It’s the small stuff that makes it happen.
Ron Ananian has been the owner of R/A Automotive in New Jersey since 1978. His radio show, “Ron Ananian, The Car Doctor,” (www.cardoctorshow.com) is syndicated in 200 markets. The podcast of the show is available on all major streaming platforms.
The articles and other content contained on this site may contain links to third party websites. By clicking them, you consent to Dorman’s Website Use Agreement.
Participation in this forum is subject to Dorman’s Website Terms & Conditions. Please read our Comment Policy before commenting.