Customer satisfaction surveys should be clear, concise, and targeted.
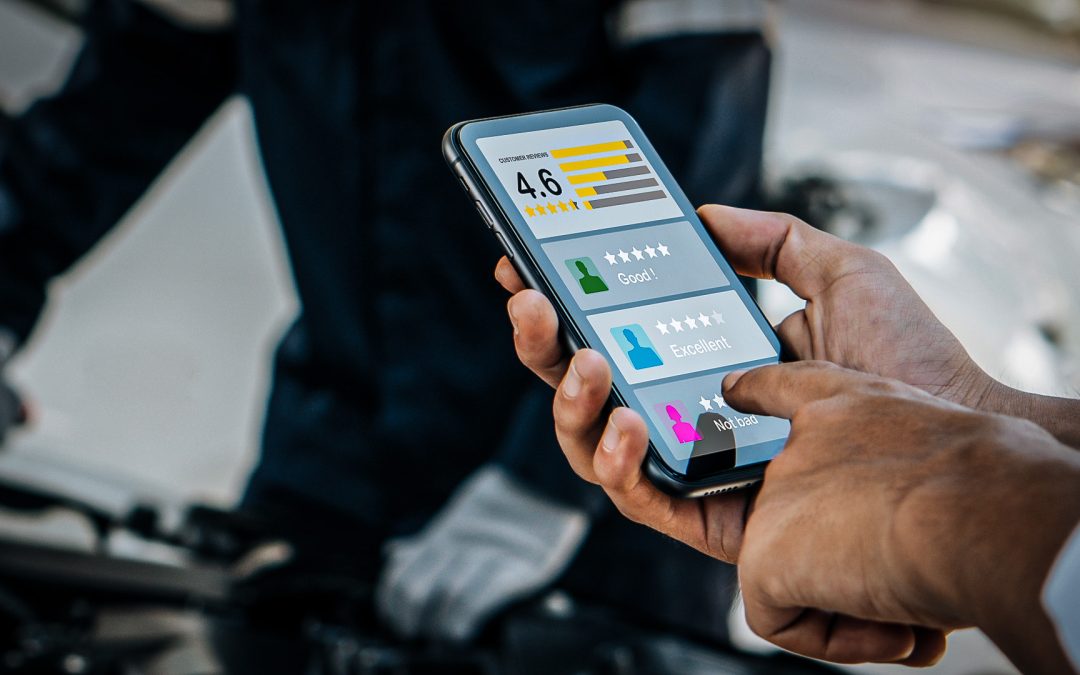
If you’re not welding an exhaust but instead clamping it in, clock your clamps. By this, I mean index them in a way that makes sense. Most of the time, I see the nuts of the clamp pointing straight down, and in many cases, that is OK.
For instance, if a tailpipe joins a muffler and the muffler body hangs lower than the clamp’s lowest point, that orientation is fine. But on some vehicles, the clamp’s threaded portions can actually reduce ground clearance and do make it (slightly) more likely something could snag something on the road surface.
Here note the acute problem, which is the broken exhaust, and the contributing factor which helped cause that problem: the bottomed-out springs. Photo: Lemmy.
Turning them upright sometimes is a good answer, but on some vehicles this may put the hardware uncomfortably close to the body of the car. Sometimes clocking them to 3 or 9 o’clock works well. (And actually sometimes just a hair beyond that is the move, to account for a saddle that may have been built extra-beefy if it has a lot of metal on it.)
The reason we see this most often is so the tech can get in there and blast the nuts on with an impact tool quickly. On something that sits up high, like a 4×4 pickup, orienting clamps to facilitate this is obviously not problematic—but not everything is a 4×4 pickup.
Probably the most critical spot is from behind the mufflers out to the tailpipe. (The exhaust tips!) This area is often visible when behind the vehicle, and especially if you’re piping a custom or high-zoot system on a collector car, the customer may have some definite opinions on the appearance of the vehicle. The aesthetic bankruptcy of a clamp that’s clocked at a weirdo angle or doesn’t have its hardware tucked facing up for an inoffensive look is likely something that will be brought up on the walkaround in your lot.
This advice is situational, of course. Indexing doesn’t help or matter in every spot. And if you can’t reasonably get your tools in there to work, that’s no good. But taking a moment to think about clearance around the whole pipe can lead to a better installation that doesn’t take longer.
I’m not sure why this is, but I often have exhausts come to me that have spring bolts that have been solidly bottomed when installed. If you’ve been in the game a while, you probably understand that spring bolts are used in conjunction with some variation of ball-flange joint to allow the exhaust to flex and pivot somewhat independently of the engine and chassis.
Since the hanger sits lower than the lowest point of the clamp, this clamp is fine as it is. Note there’s not really a ton of room between the pipe and body of the vehicle until the resonator section of the exhaust. Photo: Lemmy.
This is by design—if the exhaust is rigidly mounted to itself and to an engine and body that both have rubber cushioning, then it doesn’t take much motion to stress and break what is effectively an eight-foot thin-wall tube. Those flanged sections allow the pieces of the exhaust to move independently of one another, letting the exhaust truly work as a system.
Now, many vehicles do not have a spec listed for these bolts … but use your noodle! The clamps obviously need to be tight enough to prevent leaks, but loose enough for the exhaust to move. When in doubt, hook up your exhaust hose, fire up the car, and start snugging the nuts evenly until it doesn’t leak when still or when moving around.
I certainly won’t tell you I’ve never dropped my hood and just prayed enough liquid metal would pool in the right spot long enough to get some jalopy quieted down for a few more miles. I have. (And worse!) But I knew it was the wrong thing to do, just like you probably do. And I’ve also had those jobs come back, even when they kinda-sorta worked.
When welding most exhaust pipe on passenger vehicles, the top third of the pipe or so is often tight enough to the body of the car that prepping and welding a pipe properly simply cannot be done. Can you reallllllly fit your wire wheel or flap disc up there to get to bare, bright metal?
“No” is probably the answer.
Welding an exhaust under a vehicle isn’t always the best option or thing to do. Photo: Mike Apice.
So do it right. Attach the new pipe to the old, get it fitted up nicely, and stitch everything in place. (On most sub-3-inch exhausts, I like to use two half-inch stitches each beginning about 120 degrees from one another.)
Drop the whole assembly, prep all 360 degrees of the pipe, and then make your weld. Yes, it takes a minute to hang the system again, but if you ain’t got time to do it right, you’ll have to make time to do it twice, as the old saying goes.
And of course, this carries the added benefit of isolating the car from the voltage the welder produces if not using the GMAW process.
This isn’t meant to be a comprehensive article, of course, but hopefully one or two of these tips are something you are already doing or something you might want to try during your next exhaust job.
The articles and other content contained on this site may contain links to third party websites. By clicking them, you consent to Dorman’s Website Use Agreement.
Participation in this forum is subject to Dorman’s Website Terms & Conditions. Please read our Comment Policy before commenting.