Four proven ways to run a tighter ship at your shop.
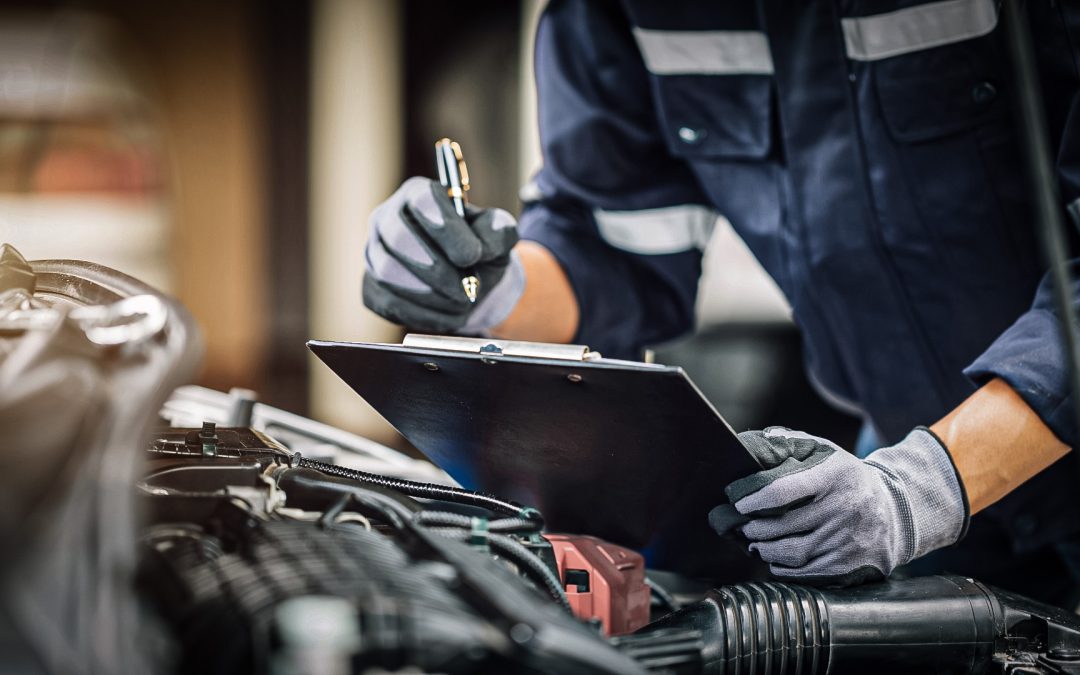
I would like to start this article off by mentioning that yes, I know air impacts are slowly going out of style—which is exactly why you might want to keep this tip in the back of your head. Parts availability can be a challenge for some old impact wrenches, and even if they can be sourced, it’s often not worth the time it takes to renew the tool. So if you have a get-it gun that’s losing its mojo, there’s a half-baked method you can employ to coax some additional (albeit very temporary) life out of it.
Often impact guns lose efficacy when the rotor vanes wear. They’re really not unlike rotor tip seals in a rotary engine, or piston rings in a standard engine. Rust (from water that your inline filter didn’t catch) and debris in the air get into your gun and slowly wear away the vanes, which are often made of a phenolic polymer and seal against the metal housing. Or in your case, stop sealing.
The solution is a rebuild or a new tool. (Or jacking up the line pressure, but that might be part of what got you into this pickle in the first place.) But that doesn’t help much when you’re trying to nurse your ailing rattle-blaster through one more week of rotations until the nice man on the tool truck arrives at your shop.
So do the same thing we do for an ailing engine that’s getting a wet compression test: throw a shot of oil down the hatch. Skip the air-tool oil; that ain’t gonna help much. You want to shove some thick stuff into the air inlet. I work on a ton of Harley-Davidsons, so SAE 60 or 20W50 is always on the shelf, and that stuff usually bumps the power back up to acceptable levels to get by for a little longer.
The articles and other content contained on this site may contain links to third party websites. By clicking them, you consent to Dorman’s Website Use Agreement.
Participation in this forum is subject to Dorman’s Website Terms & Conditions. Please read our Comment Policy before commenting.