Four proven ways to run a tighter ship at your shop.
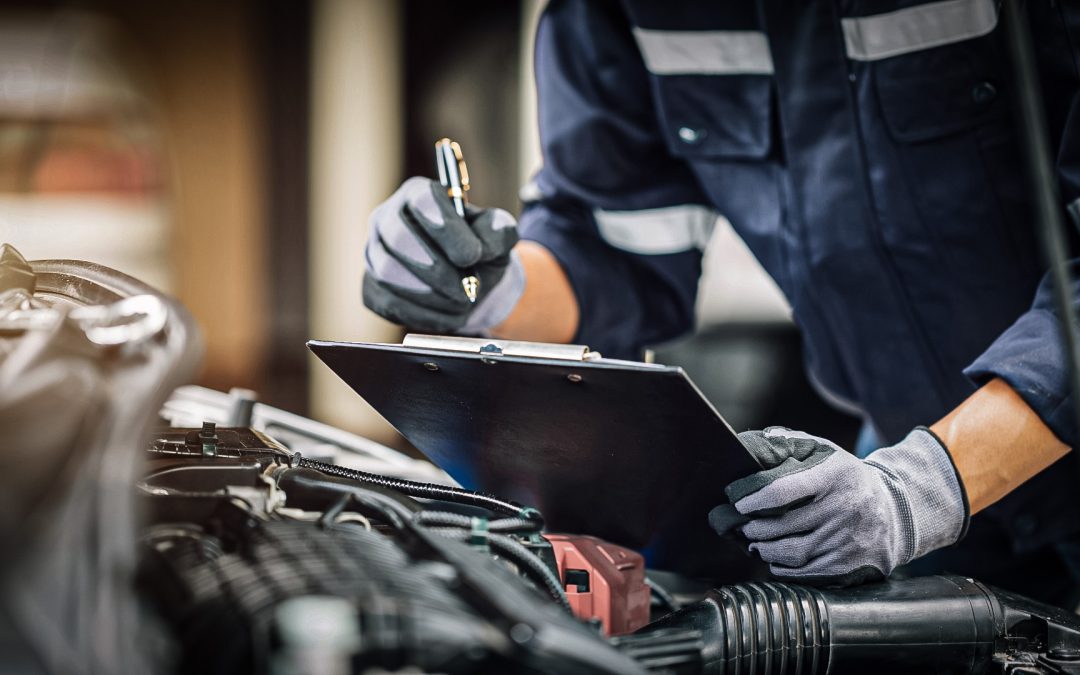
A vehicle recently came to me that made me feel pretty terrible. The customer was not happy, and I know for a fact the shop lost money on the job, so presumably they were unhappy, too. The vehicle—and scenario—seemed ripe for a quick story, because there were so many things that could have gone better on such a small job. Effectively, a few mistakes were made, and shop and customer alike both wound up unhappy. I suppose it’s also timely since this is related to sparkin’ plugs and hot on the heels of Pete’s excellent spark plug service article we ran not long ago. Here’s what transpired:
The customer brought this vehicle to a small independent shop for a checkover prior to taking a long trip and signed a work order for $50. The vehicle was running OK, and was slated for pickup a few hours later.
Upon arriving for pickup, the customer was informed that several ignition-related repairs needed to be made as the car was not running correctly. This caused a delay in the car being finished on time, and the customer was forced to wait while several rounds of parts showed up. Understandably, the customer was not pleased and didn’t want to be charged for repairs since the vehicle was not dropped off with any driveability issues. Unsurprisingly, the customer declined any repairs.
When the car arrived, this is what I found:
Hmm. New parts here, and on different cylinders. Wonder what that means. Photo: Lemmy.
I spied a brand-new coil on Cylinder 3 there, and a brand-new harness (maybe a 645-940?) on Cylinder 2. I get nervous when I see something has been worked on and now it’s my vehicle to repair. Those jobs sometimes get sticky; sometimes there was a pretty good tech working before me!
As I assessed, this was the story that began crystallizing in my mind: I suspect the tech removed plugs for inspection, which is supported by the fact that the customer was quoted plugs.
I’d be impressed if the tech was checking compression or wanted to monitor the health of every cylinder. More realistically, I would bet he and the service writer assumed a basic plug job was something the customer was going to approve, so they stayed out.
The customer was called, declined the job, and was probably told then to come pick up the vehicle. Good for the service writer and tech for working efficiently. The mechanic put it back together, and I bet the car threw a code at this point.
So now the customer is on the way, and the car now has a very noticeable CEL that was not illuminated when the car was dropped off. Unlucky, but it happens to all of us. “It was working when I dropped it off” is not a new utterance.
I would like to think the best of this mechanic, and the car did not display a P0302, which would indicate #2 was the faulty hole. Or perhaps it did, and he misidentified the cylinder. So at this point, I think this fella said, “Well, the coil musta died, better get one coming.” He tells the service writer to get a coil with the car (and customer) sitting, awaiting parts.
It’s odd that two cylinders were involved in the repair. Now I hope he saw a P0300, because that’s harder to assess. (OK, not really hard, but it’s another opportunity to explain what I saw in front of me while assuming the best of the mechanic.) I would have expected this car to have exhibited a P1305 code—I’ll get to that in a moment.
I have to ask myself, “Self, why was the customer waiting for a coil to show up? We have a diagnostic tool we can use in all the other holes: the other coils.” In fact, in a pinch, I think this car could have been diagged correctly without a scanner at all. Were this me and I suspected a bad coil, I would just move two coils and see if the miss moved or stayed put.
But I want to give this technician the benefit of the doubt. Maybe it was indeed a P0300 code and he couldn’t isolate the misbehaving cylinder—or so he thought. In a low-tech way, he coulda started pulling coil harnesses. The one that doesn’t affect engine RPM (or stall the car out entirely) is the hole that isn’t operating correctly and probably would be a good starting point for investigation and inspection.
I’ve checked for misses by simply using a temp probe or a spray bottle full of water on the exhaust manifold to see which cylinder isn’t firing. An old-timey trick, but perhaps this wrench is younger than I am.
But our tech did not do that. He stabbed that coil in, I think, and it didn’t fix the problem. Shop cost on that coil was probably right around $40. And the part didn’t fix the car. And the customer is in the shop pacing.
And now the tech is continuing to diag. Maybe by now he saw a broken wire. Or maybe he broke out his multimeter and finds the harness bad. I’m assuming he wasn’t using a scope, but instead checked for power and ground and left the other two wires of this four-wire harness intact.
Remember when I wondered before if the car did not show a P1305? That’s a different code and to me, says the problem is upstream of the plugs and coil, personally, and also how I’ve seen bad harnesses manifest themselves (other than the miss, of course.)
So the customer waits while a new harness ($10 or so) is delivered, and then waits more while the tech wires it in. I believe all four spark plugs were out of the car, because when I pulled them, they were obviously overtorqued. All of them had their gaskets squished flatter than a pancake. They were in there so tight I had to switch to an 18” ratchet to generate the leverage needed to spin ‘em free.
But here, to me, is the kicker: the tech replaced a coil before a consumable. Look at these plugs, which were all in the same shape.
That plug is plumb tuckered out. And the crush washer has been…uh, fully crushed. Photo: Lemmy.
Spec on these plugs is .043”. The plugs looked good except for being badly eroded (and thus a great recommendation from the mechanic). All measured at .060” or so, well outside of what I’d expect to perform well. Frankly, I’m surprised the car was still running as well as it was. I’m also not a fan of how sacked those crush washers are. I’m not sure why they were all torqued down so hard, but here we are.
I would never attempt diagnosing a driveability issue on plugs like this, but the car did roll out under its own power and not missing. I put a set of plugs in the car and sent it on its way—but it was educational as I thought through the process the previous tech must have undergone.
I do think it might have made sense to show the customer the plugs and explain what happened. That’s what I did, and I sold the parts this shop should have sold in the first place. Instead, the shop spent as much on parts as they charged to complete the job, yet there was no chance at recouping those costs. In fact, assuming the tech was paid for any portion of this job, the business lost money. If nothing else, I do admire them for making the car right for the customer, even to their own financial detriment.
I can’t speak for you, but for me, this car served as yet another reminder that keeping things simple really does make sense.
The articles and other content contained on this site may contain links to third party websites. By clicking them, you consent to Dorman’s Website Use Agreement.
Participation in this forum is subject to Dorman’s Website Terms & Conditions. Please read our Comment Policy before commenting.